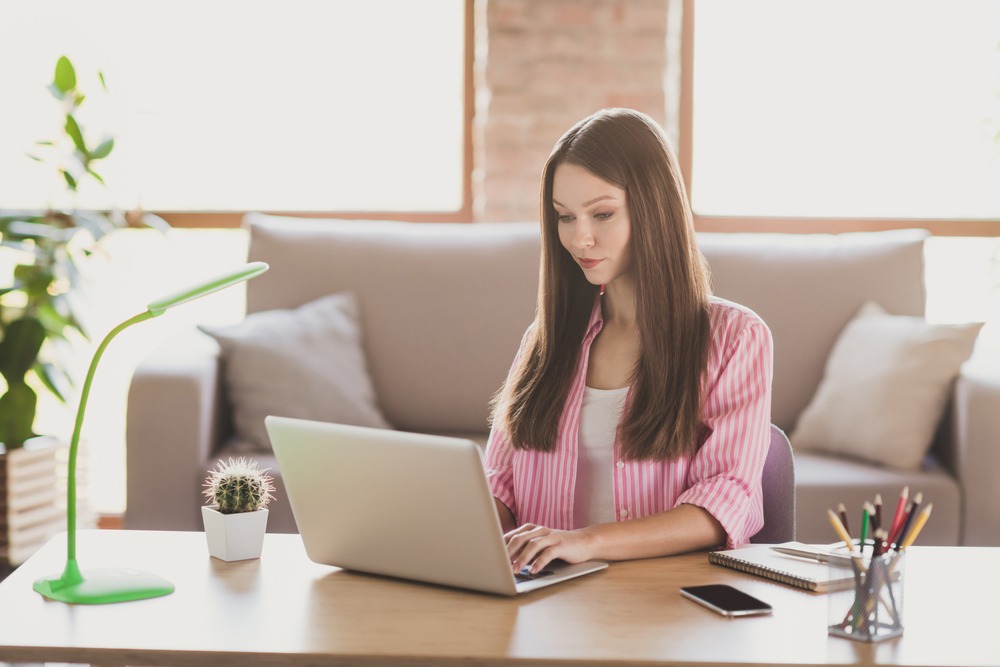
Inventory management is a cornerstone of business operations, essential for tracking and managing inventory levels to facilitate the smooth flow of goods from manufacturers to consumers. It encompasses various processes, such as demand forecasting, inventory tracking, ordering, and storage management. These processes are critical for maintaining a balance between supply and demand.
Effective inventory control plays a pivotal role in business success by ensuring that products are available when customers need them while minimizing excess costs related to storage and waste. With proper inventory management, businesses can achieve several key objectives:
Cost Reduction: By optimizing stock levels, companies can significantly reduce the costs associated with holding excess inventory.
Improved Cash Flow: Timely order fulfillment leads to better turnover rates and reduced stockouts, enhancing cash flow.
Customer Satisfaction: Accurate and prompt order fulfillment meets customer demands effectively, fostering trust and loyalty.
Through strategic techniques and systems, businesses can maintain optimal inventory levels, which reflects positively on their operational health.
For instance, Rentopian, an all-in-one software for event and party rental business operations, offers valuable insights into how effective inventory management can streamline rental processes. Their platform not only helps in managing but also in growing rental businesses through features like affiliate programs which allow users to earn ongoing commissions by referring other rental companies to use Rentopian’s software.
As you delve into “Inventory Management 101: Types, Benefits, and Techniques,” understanding these foundational aspects will provide a comprehensive insight into why effective inventory management is indispensable for thriving business operations.
Types of Inventory Management Systems
Just In Time (JIT) Inventory System
The Just In Time (JIT) inventory system is a streamlined approach that aims to minimize inventory levels by receiving goods only as they are needed in the production process. This method is designed to improve production efficiency and reduce waste by aligning inventory orders directly with production schedules.
Definition and Explanation of JIT
The JIT system revolves around minimizing excess stock and maximizing resource utilization. By ensuring that inventory arrives exactly when needed, companies avoid holding surplus stock that ties up valuable capital. JIT relies heavily on precise demand forecasting and robust supply chain coordination to function effectively.
Advantages of JIT in Reducing Excess Stock
Cost Savings: By limiting unnecessary stock, businesses significantly cut down storage costs and reduce waste associated with unsold products.
Improved Cash Flow: Companies can allocate financial resources more effectively, spending on other operational needs rather than maintaining large inventories.
Enhanced Product Quality: With fresher inputs arriving regularly, the risk of using outdated or damaged materials diminishes, leading to higher quality products.
Flexibility and Responsiveness: Businesses can quickly adapt to changes in demand without being hampered by pre-existing excess stock.
Examples of Industries That Benefit from JIT
Several industries thrive under the JIT model due to its efficiency-driven nature:
Automotive Manufacturing: Toyota pioneered the use of JIT, dramatically improving their production processes and setting a standard for automotive production worldwide.
Electronics Manufacturing: With frequent technological advancements, electronics manufacturers benefit by keeping minimal inventory to stay current with new developments.
Retail Fashion: Fast fashion brands utilize JIT to rapidly respond to changing fashion trends, ensuring they keep pace with consumer demands while minimizing unsold stock.
Incorporating a JIT inventory system requires a high degree of coordination across supply chains and precise demand forecasting. Yet, when executed correctly, it leads to remarkable efficiencies and cost savings.
However, it’s not just traditional industries that can benefit from such systems. For instance, businesses in the event rental sector can also leverage these principles. By implementing an online booking system, they can streamline their operations further, ensuring that inventory is managed efficiently and effectively.
Moreover, with the right tools such as event rental software, these businesses can automate various processes, reducing manual errors and saving time.
As you explore different inventory management systems in this guide, understanding the principles behind JIT will provide insights into how modern businesses optimize their operations for maximum productivity.
Economic Order Quantity (EOQ) Model
The Economic Order Quantity (EOQ) model is a fundamental concept in inventory management, designed to help businesses determine the optimal order quantity that minimizes total inventory costs. This includes costs related to ordering and holding stock.
The EOQ model serves as a critical tool for ensuring production efficiency and cost-effectiveness. By calculating the precise amount of inventory needed, companies can avoid overstocking or understocking, thus maintaining balance.
Benefits of EOQ
Cost Minimization: EOQ aids businesses in reducing total inventory costs by balancing ordering and holding expenses.
Improved Efficiency: With an optimal order quantity, companies streamline their operations, ensuring resources are not wasted on excessive stock.
In practice, you’ll find the EOQ model applied across various industries where managing inventory levels is crucial. For instance:
Manufacturing firms use EOQ to align raw material orders with production schedules.
Retail businesses utilize it to maintain adequate stock levels without incurring high storage costs.
By integrating the EOQ model with other systems like the JIT inventory system, cycle counting process, or perpetual inventory tracking, businesses can fine-tune their strategies further. This synergy enhances not only inventory management but also the overall operational health of an organization.
- ABC Analysis Technique for Inventory Categorization
ABC analysis is a strategic approach within inventory management that categorizes inventory into three classes: A, B, and C. This technique helps businesses prioritize management efforts by focusing on high-value items, ensuring that resources are allocated efficiently.
1. Class A
These items represent the most valuable segment of your inventory. They typically account for a small proportion of the total stock but contribute to a large percentage of the overall value. Prioritizing these items is crucial as they have a significant impact on your business’s profitability and require close monitoring and regular review.
2. Class B
This category includes items that fall between the high-value A class and the lower-value C class. Class B items are moderately important, contributing to a reasonable portion of the sales volume or value. Businesses should manage these items with moderate control and attention.
3. Class C
Representing the least valuable inventory items, Class C often constitutes a large portion of stock numbers but only a small percentage of the overall value. These items can be managed with less stringent controls compared to Class A and B, as they have less impact on financial performance.
Prioritizing high-value items through ABC analysis allows businesses to allocate resources effectively, directing attention where it’s needed most. Strategies for managing each category include:
For Class A, implement tight controls, frequent stock reviews, and detailed demand forecasting.
For Class B, maintain balanced controls and periodic reviews.
For Class C, utilize automated systems to reduce manual intervention while ensuring availability.
Integrating the ABC analysis technique with other methods such as JIT inventory system or EOQ model enhances production efficiency and optimizes inventory levels across different categories.
Cycle Counting Process for Inventory Accuracy Verification
Cycle counting is a dynamic inventory management approach that emphasizes continuous verification of stock accuracy rather than relying on infrequent, large-scale physical counts. This methodology involves regularly counting a subset of inventory items on a rotating schedule, allowing businesses to maintain high levels of accuracy in their inventory records.
Overview of Cycle Counting Methodology:
Selection Criteria: Items are selected based on various criteria, such as transaction frequency, value, or the last counted date. This ensures that critical items are reviewed more frequently.
Counting Schedule: The process is typically integrated into daily or weekly operations, with different cycles for different item categories. For instance, high-value or fast-moving items may be counted more often than low-value or slow-moving ones.
Discrepancy Analysis: Identified discrepancies between recorded and physical stock levels trigger an immediate investigation. This helps in identifying root causes, whether they stem from data entry errors, theft, or damaged goods.
Benefits of Regular Cycle Counts:
Inventory Accuracy: By regularly verifying stock levels, businesses can maintain accurate inventory records, which are crucial for efficient operations and decision-making.
Reduced Disruptions: Unlike complete physical inventories that require halting operations, cycle counting allows businesses to continue normal activities without major disruptions.
Cost Efficiency: Continuous monitoring through cycle counting reduces the need for extensive full-scale counts and minimizes labor costs associated with large inventory audits.
Enhanced Production Efficiency: Accurate inventory data supports other systems like the JIT inventory system, EOQ model, and ABC analysis technique, ensuring production runs smoothly with minimized excesses.
Incorporating cycle counting into your inventory management practices provides a proactive approach to maintaining stock accuracy and optimizing overall efficiency.
Periodic Inventory Method with Counting Intervals Defined
The periodic inventory method is a traditional approach to inventory management where counts are conducted at specific intervals. Unlike the perpetual inventory tracking system, this method updates inventory records periodically rather than continuously. Typically, businesses perform these counts quarterly, semi-annually, or annually, depending on their operational requirements and resource availability.
How It Works:
Businesses halt operations temporarily to conduct physical counts of their entire inventory.
These counts are then compared against recorded data to identify discrepancies.
Adjustments are made to reflect the accurate stock levels in financial records.
This system is relatively straightforward and less costly regarding technology requirements compared to methods like the JIT inventory system or EOQ model. However, it relies heavily on manual processes, making it labor-intensive.
Potential Challenges:
Time Gaps Leading to Inaccuracies: With intervals between counts, discrepancies can accumulate unnoticed. This delay may lead to inaccurate stock levels in records until the next count cycle.
Resource Intensive: Scheduled counts require significant manpower and can disrupt normal business operations during the counting period.
While the periodic inventory method offers a structured framework for managing stocks without substantial technological investment, it may not provide the real-time accuracy needed by industries with high transaction volumes or complex supply chains. For businesses seeking more precise control over their stock levels, exploring alternatives such as the ABC analysis technique, cycle counting process, or the more advanced perpetual inventory tracking might be beneficial.
Understanding the Perpetual Inventory Tracking System with Real-Time Updates
Perpetual inventory tracking systems represent a modern approach to inventory management by providing continuous updates on stock levels through every transaction. Unlike the periodic inventory method that relies on scheduled counts, perpetual systems automatically adjust inventory records each time goods are received, sold, or returned. This real-time update capability enables businesses to maintain accurate and up-to-the-minute data on their inventory status.
Advantages of Perpetual Inventory Systems:
High Transaction Volumes: Businesses dealing with high transaction volumes benefit significantly from perpetual systems. Retailers and large-scale distributors often require precise stock information to handle frequent sales and replenishments efficiently.
Complex Stock Management: Companies with intricate product lines or multiple warehouses find perpetual tracking invaluable. It ensures seamless synchronization across various locations, reducing discrepancies and improving overall coordination.
Improved Decision-Making: Access to real-time data aids in making informed decisions regarding purchasing, production scheduling, and demand forecasting. This is particularly beneficial when implementing strategies like the JIT inventory system or optimizing via the EOQ model.
Reduced Stock Discrepancies: Continuous updates minimize errors associated with manual entries and delayed record-keeping found in other methods like the periodic inventory method. This accuracy is crucial for preventing issues related to stockouts or overstocking.
Incorporating perpetual inventory tracking aligns well with advanced techniques such as ABC analysis and the cycle counting process, enhancing overall production efficiency. By ensuring precise control over stock levels, businesses can minimize excess costs while maintaining optimal readiness for customer demands.
Benefits Derived from Effective Inventory Management Practices
Cash Flow Optimization Through Timely Order Fulfillment
Efficient inventory management practices are crucial for enhancing a business’s cash flow. By ensuring timely order fulfillment, businesses can maintain better cash flow, which is essential for sustaining operations and facilitating growth. Here’s how effective inventory management contributes to cash flow optimization:
Improved Turnover Rates: By maintaining optimal inventory levels, businesses can increase their turnover rates. This means products are sold and replenished more frequently, leading to a steady stream of revenue. Higher turnover rates reduce the risk of holding outdated or unsellable stock, freeing up financial resources that would otherwise be tied up in stagnant inventory.
Reduced Stockouts: Efficient inventory management helps prevent stockouts, situations where demand exceeds supply and sales opportunities are lost. Stockouts not only result in immediate lost sales but can also damage customer trust and satisfaction. With proper tracking and forecasting, companies can avoid these scenarios, ensuring they have adequate stock on hand to meet customer demand.
Minimized Waste: By fine-tuning inventory levels and employing techniques like Just In Time (JIT) or Economic Order Quantity (EOQ), businesses can minimize waste due to overproduction or obsolescence. Less waste translates directly into cost savings, allowing those funds to be redirected towards other critical areas of the business.
Efficient Use of Storage Space: Managing inventory effectively means using storage space judiciously. Warehousing costs can be significant, and by keeping inventory at optimal levels, businesses can reduce these expenses considerably. This reduction in operational costs is a key component of cash flow optimization.
Enhanced Supplier Relationships: Reliable inventory management fosters better relationships with suppliers through timely payments facilitated by consistent cash flow. Strong supplier relationships often lead to favorable terms such as discounts or extended credit periods, further enhancing cash reserves.
The relationship between effective inventory management and cash flow is clear—it supports a cycle where reduced operational costs and minimized waste create opportunities for reinvestment and growth. Embracing robust inventory strategies as part of your approach to Inventory Management 101: Types, Benefits, and Techniques ensures you stay competitive while optimizing your financial health.
Enhanced Customer Satisfaction Metrics Achieved Via Accurate Order Fulfillment Processes
Effective inventory management plays a crucial role in elevating customer satisfaction metrics by ensuring timely and accurate order fulfillment. Meeting customer demands promptly is a direct result of well-structured inventory practices that align product availability with consumer expectations.
Here are some ways how effective inventory management enhances customer satisfaction:
Reduced Operational Costs: By optimizing inventory levels, businesses lower holding costs, minimizing waste from unsold goods. This efficient management translates to better pricing strategies, which can enhance customer satisfaction.
Timely Order Fulfillment: Accurate inventory tracking ensures that products are readily available when customers need them, reducing delays and avoiding stockouts. This reliability builds trust and loyalty among consumers.
Cash Flow Optimization: Efficient systems facilitate better turnover rates, allowing businesses to reinvest in quality improvements and customer service enhancements. This cycle supports a positive customer experience.
In the realm of Inventory Management 101: Types, Benefits, and Techniques, understanding how these elements interconnect is vital for any business aiming to boost its reputation through superior service delivery. Keeping customers satisfied not only minimizes lost sales but also fortifies brand loyalty in competitive markets.
Stockout Prevention Strategies That Minimize Over-Stock Consequences
Effective inventory management is crucial for maintaining a balance between having enough stock to meet customer demands and avoiding excess that ties up capital. This balance results in reduced operational costs and minimized waste from unsold goods. Stockouts, which occur when items are unavailable for sale, can lead to lost sales and diminished customer trust. Conversely, overstocking incurs additional costs related to storage and depreciation.
Proper Tracking Techniques:
Demand Forecasting: Accurate demand forecasting helps predict customer needs, ensuring timely order fulfillment without surplus.
Real-Time Inventory Tracking: Utilizing systems like the Perpetual Inventory System provides continuous updates on stock levels, preventing both shortages and surpluses.
Reorder Point Calculation: Establishing precise reorder points ensures inventory is replenished at the right time, optimizing cash flow.
Safety Stock Management: Maintaining an optimal level of safety stock acts as a buffer against unexpected demand spikes or supply chain disruptions.
These strategies not only prevent stockouts but also help in achieving cash flow optimization by ensuring resources are efficiently utilized. As part of the “Inventory Management 101: Types, Benefits, and Techniques,” mastering these practices is essential for lowering holding costs and promoting sustainable business operations.
Challenges Faced in Implementing Effective Inventory Management Techniques
Supply Chain Issues Impact on Inventory Management Systems
Inventory management systems face significant challenges due to the complex and often unpredictable nature of supply chains. External factors, such as global events, can cause severe disruptions that ripple through the entire chain, affecting inventory levels and management strategies.
Global Events and Their Effects:
Natural Disasters: Earthquakes, floods, and hurricanes can damage infrastructure and halt production lines, leading to delays in the delivery of goods. These disruptions require businesses to adjust their inventory levels quickly to prevent stockouts.
Economic Instability: Fluctuations in currency values or economic sanctions can impact suppliers’ ability to deliver goods, thus affecting inventory availability. Businesses may need to find alternative suppliers or adjust pricing strategies to maintain inventory flow.
Political Unrest: Political instability can result in border closures or trade restrictions, interrupting the supply chain. Companies must be agile enough to shift their sourcing strategies and manage inventory accordingly.
Ripple Effects on Inventory Management:
Demand Variability Challenges: Sudden changes in consumer demand due to these external events can lead to either excess inventory or shortages. Effective demand forecasting and flexible inventory systems are crucial for adapting to these shifts.
Logistical Delays: Transportation issues arising from global disruptions can delay shipments, affecting lead times and increasing holding costs. Utilizing technology like real-time tracking systems can help mitigate some of these delays by providing visibility into shipment status.
Supplier Reliability Concerns: When suppliers face their own challenges, it impacts their reliability and consistency in delivering goods. Establishing strong relationships with multiple suppliers can provide a buffer against such uncertainties.
Strategies for Mitigating Supply Chain Impacts:
Diversifying Suppliers: Reducing dependency on a single supplier or region by sourcing materials from multiple locations helps spread risk.
Technology Integration: Implementing advanced technologies like AI-driven analytics can improve forecasting accuracy and enable proactive adjustments to inventory levels based on predictive insights.
Buffer Stock Maintenance: Maintaining a strategic reserve of critical components or finished products allows businesses to continue operations during supply chain interruptions.
Moreover, it’s essential for businesses involved in event rentals to consider specific factors that could impact their operations, such as implementing an effective damage waiver policy which is crucial for mitigating losses during unforeseen circumstances like natural disasters.
By understanding these challenges and implementing robust strategies, businesses can enhance their resilience against supply chain disruptions, ensuring smoother operation of their inventory management systems. A proactive approach not only mitigates risks but also positions businesses better for future growth opportunities amidst global uncertainties.
Addressing Inaccuracies Found Within Stock Records Maintained Over Time
In the world of inventory management, stock record inaccuracies pose significant challenges. These discrepancies often come from various sources:
Data entry errors during manual stock counts.
Misplaced or mislabeled items, making it difficult to track inventory.
System integration issues where different software tools fail to work together effectively.
Importance of Regular Audits
Regular audits emerge as a vital solution to maintain accuracy. Conducting frequent checks helps identify and fix errors quickly, ensuring data integrity across systems.
Dealing with Demand Variability Challenges
Demand variability challenges make these issues worse. Unpredictable consumer behavior can lead to unexpected changes in stock levels, making planning strategies more complicated. Businesses must adapt by using advanced forecasting models and analyzing past data to predict trends more accurately.
Implementing Technologies for Improvement
To solve stock record inaccuracies, using technologies like barcode scanning and RFID tags can greatly improve precision and efficiency. Automated systems reduce human error and provide real-time updates, following best practices outlined in Inventory Management 101: Types, Benefits, and Techniques.
The Bigger Picture: Why Accurate Stock Records Matter
Keeping accurate stock records is not just about reducing mistakes; it is about making informed decisions, optimizing resource allocation, and improving overall operational efficiency. By directly addressing these inaccuracies, businesses can better navigate the complexities of inventory management and supply chain dynamics.
FAQs (Frequently Asked Questions)
What is inventory management and why is it important?
Inventory management involves overseeing the ordering, storing, and use of components that a company uses in the production of the items it sells. Effective inventory control is significant for business operations as it helps minimize costs, optimize cash flow, and ensure timely order fulfillment.
What are the different types of inventory management systems?
There are several types of inventory management systems including Just In Time (JIT), Economic Order Quantity (EOQ) model, ABC analysis technique, cycle counting process, periodic inventory method, and perpetual inventory tracking. Each system has its own advantages and is suited to different business needs.
How does the Just In Time (JIT) inventory system work?
The JIT inventory system minimizes inventory levels by ordering goods only as they are needed in the production process. This approach reduces excess stock and improves production efficiency, making it beneficial for industries such as manufacturing and retail.
What is the purpose of the Economic Order Quantity (EOQ) model?
The EOQ model helps businesses determine the optimal order quantity that minimizes total inventory costs, including ordering and holding costs. It provides a formula that assists companies in managing their stock levels effectively.
What benefits can businesses derive from effective inventory management practices?
Effective inventory management can lead to reduced operational costs, minimized waste, optimized cash flow, and timely order fulfillment. These practices enhance customer satisfaction by ensuring accurate order fulfillment and preventing stockouts.
What challenges do businesses face when implementing effective inventory management techniques?
Challenges include demand variability, supply chain issues that impact inventory levels, and inaccuracies found within stock records over time. Addressing these challenges requires regular audits and adaptive planning strategies to maintain accuracy and efficiency.